Revolutionizing Battery Manufacturing: Atlas Power Technologies’ NMP-Free LFP Slurry Process
Atlas Power Technologies has introduced a groundbreaking innovation in lithium-ion battery manufacturing: a water-based, NMP-free electrode process. This technology enables the production of ultra-thick electrodes (160 µm), offering areal capacities exceeding 4 mAh/cm². With this sustainable and scalable solution, Atlas aims to transform battery production, reduce costs, and enhance environmental safety, all while maintaining superior performance.
The Problem with Traditional Methods
Traditional electrode manufacturing relies on N-methyl-2-pyrrolidone (NMP), a toxic solvent. NMP increases production complexity, raises costs, and brings regulatory challenges due to its hazardous nature. Moreover, electrodes made using solvent-based processes are prone to cracking or delamination at higher thicknesses. These limitations hinder the scalability and efficiency of current battery production methods.
A Sustainable Breakthrough
Atlas Power Technologies’ water-based, NMP-free process eliminates the need for harmful solvents. Instead, this method uses a water-based slurry that ensures environmental safety without compromising on quality. This process delivers high-performance electrodes with superior mechanical integrity, even at ultra-thick dimensions.
Key Advantages of Atlas’s Technology
This innovation offers several critical benefits, ensuring that battery manufacturers can adopt it seamlessly:
- Cost Reduction: By eliminating NMP, manufacturers can lower capital expenditure by up to 25% and reduce overall production costs by 15%.
- Scalability: Atlas’s water-based process integrates easily with existing gigafactory setups, avoiding the need for costly new equipment.
- Performance Retention: The process achieves performance levels comparable to traditional PVDF-NMP methods while avoiding the use of toxic solvents.
- Sustainability: Water-based production significantly reduces environmental risks, ensuring compliance with stringent regulations.
- Enhanced Electrode Flexibility: Unlike conventional methods, Atlas’s process delivers electrodes that maintain structural integrity at higher thicknesses.
Exceptional Performance in Coin Cells
Atlas has validated its technology through rigorous testing, showcasing impressive results:
- LFP Half-Cell Battery Testing: The charge-discharge curves of lithium iron phosphate (LFP) coin cells prepared using Atlas’s water-based process showed comparable gravimetric and areal capacities to those prepared using traditional PVDF-NMP methods.
- LFP-Graphite Full Cells: Coin cells using graphite and LFP electrodes produced via Atlas’s method achieved areal capacities exceeding 2 mAh/cm². These cells also demonstrated excellent coulombic efficiency, proving the method’s reliability.
Compatibility with Gigafactories
One of the most notable advantages of Atlas’s innovation is its backward compatibility with existing gigafactory setups. Unlike dry-electrode manufacturing processes, which require entirely new infrastructure, Atlas’s water-based method integrates seamlessly into current production lines. This compatibility minimizes transition costs and simplifies scaling for large-scale battery producers.
CEO Insights on the Industry Impact
Mitchell Miller, CEO of Atlas Power Technologies, emphasized the transformative potential of this technology.
“This breakthrough manufacturing process is a game-changer for the industry,” Miller stated. “It offers battery producers a scalable and safer solution that will save billions while maintaining exceptional performance. Our process addresses critical industry challenges, paving the way for a more sustainable and efficient future.”
Collaboration for Commercialization
Atlas Power Technologies is actively seeking strategic partners to accelerate the adoption of its water-based NMP-free process. The company invites licensing and co-development opportunities to help battery manufacturers enhance their production capabilities, reduce costs, and future-proof their operations.
Industry Applications and Future Potential
The implications of this innovation extend far beyond cost savings. By removing toxic solvents, Atlas’s process aligns with global sustainability goals. This positions battery manufacturers to meet increasing demands for environmentally friendly production practices. Furthermore, the ability to produce ultra-thick electrodes expands the potential for high-capacity applications, including electric vehicles, grid storage, and portable electronics.
CSO Perspective on Performance Metrics
Ali Khosrozadeh, Chief Science Officer of Atlas, highlighted the technical achievements of this method.
“We have successfully demonstrated comparable performance to conventional PVDF-NMP in half-cells while reaching the theoretical capacitance of LFP,” Khosrozadeh said. “Additionally, our LFP-graphite full cells show an areal capacity above 2 mAh/cm², completely free of toxic NMP. This innovation redefines what is possible in lithium-ion battery production.”
Why This Matters for the Battery Industry
The global battery market faces mounting pressure to reduce costs, improve efficiency, and meet sustainability standards. Atlas’s water-based process addresses these challenges head-on, offering a practical and impactful solution. By adopting this technology, manufacturers can achieve:
- Regulatory Compliance: Avoid the risks associated with toxic solvents and ensure adherence to environmental regulations.
- Increased Production Efficiency: Leverage the scalability and simplicity of water-based manufacturing to optimize production timelines.
- Market Competitiveness: Reduce costs while maintaining high performance, enabling producers to remain competitive in the rapidly evolving battery industry.
A Call to Action for the Industry
Atlas Power Technologies encourages battery manufacturers to explore partnership opportunities and integrate this transformative technology. By adopting Atlas’s NMP-free process, companies can position themselves at the forefront of sustainable innovation while achieving significant cost savings.
Conclusion: NMP-Free LFP Slurry
Atlas Power Technologies has set a new benchmark for lithium-ion battery manufacturing with its water-based, NMP-free process. This innovation combines sustainability, scalability, and superior performance, making it a compelling choice for manufacturers worldwide. As the industry moves toward a greener and more efficient future, Atlas’s groundbreaking technology offers a clear path forward.
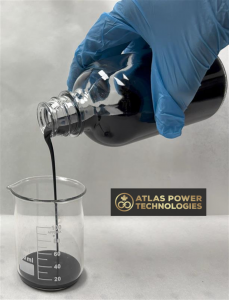
By reducing costs, enhancing performance, and prioritizing environmental safety, Atlas Power Technologies is revolutionizing the way batteries are produced—ushering in a new era of innovation and sustainability.
Key CX Takeaways for Atlas Power Technologies’ NMP-Free LFP Slurry
- Enhanced Sustainability
Atlas Power’s NMP-free LFP slurry revolutionizes customer experience by prioritizing sustainability. Traditional solvent-based methods rely on toxic N-methyl-2-pyrrolidone (NMP), which poses health and environmental risks. By adopting this water-based formulation, customers reduce their ecological footprint and align with global sustainability goals without compromising on performance. - Exceptional Performance
The NMP-free slurry offers comparable, if not superior, performance to conventional methods. With electrodes capable of achieving an ultra-high thickness of 160 µm and a theoretical areal capacity exceeding 4 mAh/cm², customers can enjoy enhanced battery efficiency. This ensures optimal charge-discharge cycles and coulombic efficiency, which directly translates to better-performing batteries for end-users. - Scalable Manufacturing
For battery producers, the slurry provides a cost-effective, scalable alternative. Unlike dry-electrode manufacturing that demands a complete overhaul of existing systems, Atlas’ water-based process is backward-compatible. This means seamless integration into existing gigafactory setups, reducing downtime, implementation complexity, and costs. - Cost Reduction Opportunities
Atlas Power’s solution helps customers reduce both capital expenditures (CapEx) and operational costs. By eliminating the need for expensive NMP solvent recovery systems, battery manufacturers can lower their CapEx by up to 25%. Additionally, production costs are reduced by up to 15%, empowering companies to maintain competitive pricing in the market. - Regulatory Compliance
Regulatory burdens associated with NMP usage are significant, often involving strict safety standards and costly waste management systems. By offering an NMP-free alternative, Atlas helps customers streamline regulatory compliance processes, cutting down on time, labor, and associated costs. This makes operations smoother and more predictable for businesses. - Flexibility and Reliability
Traditional solvent-based electrode coatings are prone to cracking or delamination, especially at higher thicknesses. Atlas’ water-based slurry eliminates these issues by providing excellent mechanical integrity and flexibility, even for ultra-thick electrodes. This ensures consistent quality, minimizing product failures and delivering a more reliable experience for customers. - Customizable Electrode Design
The NMP-free slurry allows manufacturers to produce battery electrodes with customizable thicknesses. This flexibility enables companies to design tailored solutions for diverse applications, including electric vehicles (EVs), energy storage systems, and consumer electronics. Customers gain a competitive edge by addressing specific market demands effectively.
Additional Key CX Takeaways: NMP-Free LFP Slurry
- Health and Safety Benefits
Eliminating NMP enhances workplace safety for manufacturing personnel. NMP is known for its toxicity and potential to cause long-term health problems. By adopting Atlas’ water-based process, companies demonstrate their commitment to employee welfare and create a safer work environment. - Future-Proof Technology
As environmental regulations tighten globally, the industry’s reliance on toxic solvents will face increasing scrutiny. Atlas’ NMP-free technology future-proofs battery production lines, ensuring long-term compliance with anticipated legislative changes. Customers gain peace of mind, knowing their operations are equipped to meet tomorrow’s standards. - Strategic Partnership Opportunities
Atlas is actively seeking licensing and co-development partners, providing an avenue for battery manufacturers to collaborate on cutting-edge solutions. These partnerships create a collaborative ecosystem, where customers can influence product refinements, access exclusive technologies, and stay ahead of market trends. - End-User Benefits
For end-users of batteries (e.g., EV owners, renewable energy system operators), the improved electrode performance translates to longer-lasting batteries with higher energy densities. This enhances the overall user experience by reducing charging frequency and improving the reliability of devices powered by these batteries. - Brand Differentiation
Adopting Atlas’ innovative slurry process positions battery manufacturers as leaders in sustainability and innovation. This differentiation boosts brand value, strengthens customer trust, and enhances market positioning in an increasingly eco-conscious consumer landscape. - Global Impact
The NMP-free slurry has implications far beyond individual companies. By enabling scalable, sustainable, and cost-efficient battery production, Atlas supports the global shift toward clean energy and electrification. Customers become contributors to a larger movement toward a greener, more sustainable future.
Atlas Power Technologies’ NMP-free LFP slurry offers customers a holistic blend of sustainability, performance, cost-efficiency, and adaptability, delivering an unmatched customer experience while shaping the future of battery manufacturing.